JDI Wallboard Virtual Factory Tour Reflection
Question
It is a Virtual Factory Tour Reflection.
You are expected to write a report on your experience and explain what costs JDI includes in its manufacturing overhead for the plant and how the costs are allocated to their products.
Attention should be paid to proper grammar and sentence structure. This should be treated like a professional report that you would submit to a manager.
The findings are listed in the attached documents
Company: JDI Wallboard
They use Standard Costing Inventory System.
They only account Raw material inventory and Finished Good inventory, not Work in Process Inventory
Reasons:
1. Real time financial results using Operating Statements/Tableau Dashboard
2. Instant visibility on inventory levels using Bar coding Facilities
3. Visibility using flex budgeting using Cost/Quantity Changes
Step 1:
Setting the standard quantity and cost (receiving price of raw materials, adjusting for foreign exchange, future market conditions)
Standards. Adjusted through the year (Eg. From new product, new raw material)
Process Manager enters Bill of material
Accounting enters costs
70 different Bill of Material(BOM) and cost component files
Step 2:
Purchase of material
Goods recerived, costs recorded in general ledger
Actual cost of material difference
Step 3(Production):
Production, 24/7
Bar coding system
BOM drives standard raw material quantities
Cost components file
Step 4:
Wallboard slipped on railcar or truck, scaved out of inventory and creates an invoice in the system
Step 5:
Valuation of raw material
Valuation method is FIFO
Determine most
Valuation of finished goods, using Weighted average method
Physical Count/Drone Survey
Journal Entries are done in this order of for the following headings:
1. Purchase goods/ Labour and Utilities
2. Productions
3. Sale
4. Revaluation
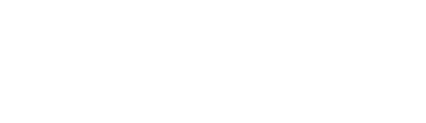
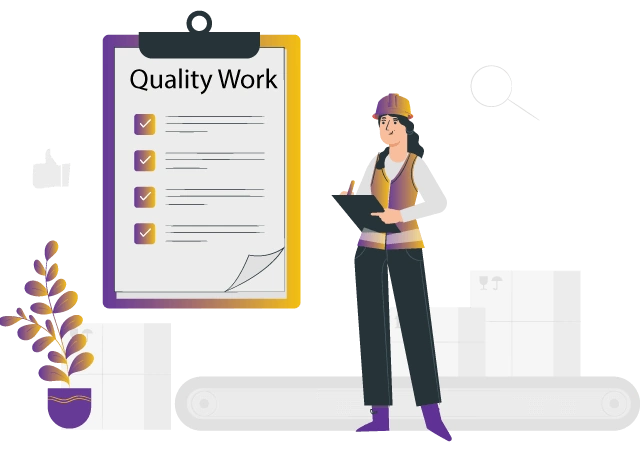
Solution
JDI Wallboard Virtual Factory Tour Reflection
The virtual factory tour of JDI Wallboard, a manufacturer that specializes in creating high-quality wallboard products, was illuminating regarding their inventory management system and manufacturing procedure. This report sheds light on how the factory's inventory management system, in particular, the use of standard costing and how it impacts its financial statements. The report also outlines the firm's inventory management method and how manufacturing overhead costs are allocated to its merchandise.
JDI Wallboard employs a standard costing inventory system, which entails setting a standard amount and pricing for raw materials and modifying it throughout the year. This enables them to obtain real-time financial information using operational statements and a Tableau dashboard. The business solely keeps track of raw material and final goods inventories; process inventories are not considered. This is due to their usage of a barcoding facility, which offers immediate visibility into inventory levels and employs flex budgeting to consider price and quantity fluctuations. Setting the standard quantity and cost, which considers the raw material receiving price, correcting for currency rates, and anticipated market circumstances is the first step in the inventory process. Next, the process manager enters the bill of materials, and accounting inputs the expenses. There are 70 separate cost components and bills of materials files for the JDI Wallboard. Following establishing the standard amount and cost, the corporation acquires the necessary materials, receives the items, and records the expenditures in the general ledger.
JDI Wallboard incorporates manufacturing overhead costs, including utilities, rent, and indirect labor, in its production process. The costs are distributed among their goods using a predefined overhead rate obtained by dividing the whole manufacturing overhead expenses by the entire allocation base. A direct labor or machine hour typically serves as the allocation base. The manufacturing overhead cost is then calculated by multiplying the actual amount of the allocation base required to make each product by the specified overhead rate. The barcoding system controls the standard raw material amounts during the continuous manufacturing process, and the cost components file calculates the exact production costs. When a wallboard is loaded into a truck, it is removed from inventory, and an invoice is generated in the system.
In conclusion, JDI Wallboard utilizes a standard costing inventory system to obtain financial data in real-time using operating statements and a Tableau dashboard. Only finished items and raw materials are included in the company's accounting; work-in-progress inventory is not. Manufacturing overhead expenses are a part of JDI Wallboard's production process and are distributed across their goods based on a specified overhead rate. The organization's inventory management system is effective, and using barcoding tools gives quick access to inventory levels.
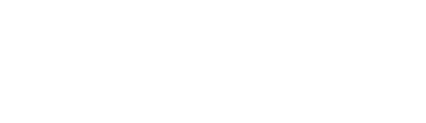
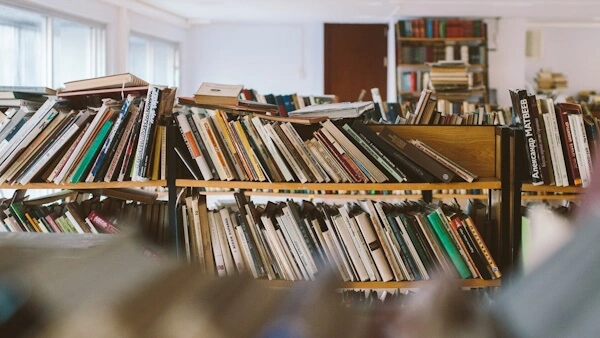

About Author
Tough Essay Due? Hire Tough Essay Writers!
We have subject matter experts ready 24/7 to tackle your specific tasks and deliver them ON TIME, ready to hand in. Our writers have advanced degrees, and they know exactly what’s required to get you the best possible grade.
Find the right expert among 500+
We hire Gradewriters writers from different fields, thoroughly check their credentials, and put them through trials.
View all writers