Six Sigma in Operations Management
Question
The topic will be "Six Sigma" in Operations Management.
1. Students will draft a term paper on an approved research topic related to field of operations management.
2. A list of suggested research topics may be found in the table below.
3. The team must gain approval from the instructor.
4. A table of contents is to be submitted to the instructor on or before the fifth session. The table of contents shall be representative of the final paper, no exceptions.
5. The paper must be written in APA format (https://apastyle.apa.org)
6. The minimum length of the paper is 6 pages. The page count starts with the Introduction and ends with the Conclusion, i.e. the body of the paper.
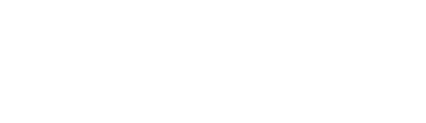
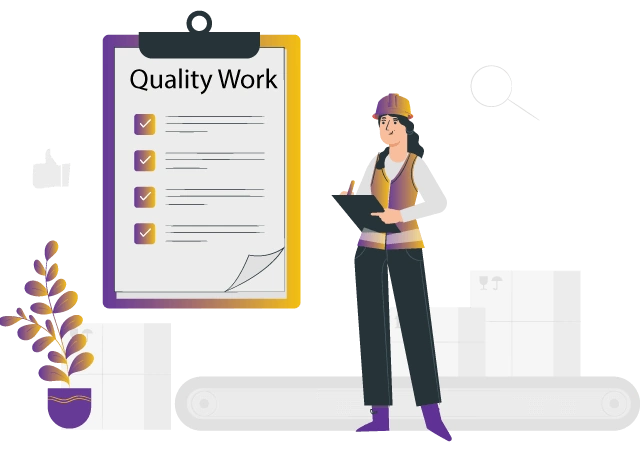
Solution
Table of Contents
Six Sigma in Operations Management 2
Six Sigma in Operations Management 2
Six Sigma in Operations Management 5
Benefits of Six Sigma in Operations Management 6
Operations Management Challenges and Criticisms. 7
Six Sigma in Operations Management
One of the main functions of an organization or a business is its operations and how they are structured. Regardless of the structure and organization used in its operation, quality is always the primary goal. Managing quality is an issue that affects both an organization and customers. Organizations are affected by the demand for increasing profits. Customers enjoy the benefit of superior products and increased functionality. Quality management is tasked with all issues related to the supply chain and the customer journey. Producers can also bolster their profit margins by increasing prices by improving quality.
There are various techniques and strategies used in managing quality. Effective tactics ensure continuity in growth because there will always be avenues for improvement. The purpose of continuous improvement is to improve an institution using quantifiable metrics that managers can implement. Six sigma refers to the techniques used in the improvement of quality. This paper extensively discusses its components, operations management functions, and impacts. Quality management in operations is implemented in both processes and products. Total quality management (TQM) is an approach to quality and its improvement in the long run; it facilitates the implementation of sustainability in operations management.
Six Sigma in Operations Management
The tools and techniques used to improve processes and outcomes constitute the six sigma concept. The domain is dynamic, and the growing customer-centricity has translated to process managers dealing with more variables. Managers optimize process quality to improve by changing their tactics. Operations management is a business domain associated with continuous improvement to increase efficiency. Limits of efficiency levels are dictated by the costs and resources used in the process. Process managers have to increase efficiencies, but that must be feasible for a business to undertake it.
Six Sigma Principles
Implementing six sigma is generally dependent on different factors. Resource availability and strategy used are the components that dictate quality. Understanding customer needs a crucial six sigma principle. Organizations rely on process and quality managers to know the variables that dictate the operations—implementing the tool requires businesses and organizations to reduce waste and increase value in processes. Using a standard methodology in process improvement ensures consistency in the process and outcome(s). Standardization is implemented in system processes using planned and strategic collaboration in quality domains. Consistency is attained by eliminating variations in the process.
Six Sigma Techniques
The adoption of six sigma requires a plan which is executed strategically. Efficiencies come from the improvements in individual processes, improving the overall outcome quality. The techniques used to implement six sigma in processes are DMAIC and DMADV. The similarity between the two is that they have a similar starting position. DMAIC is reactive as it reacts to the changes and acts against a challenge by removing it. DMADV is proactive because it prevents challenges from happening. DMAIC has definite outcomes, but DMADV is part of the desired outcome and the solution's function.
DMAIC Approach
DMAIC is a five-step process of implementing six sigma in processes. The name abbreviates the five steps; Define, Measure, Analyze, Improve and Control steps (Shankar, 2009). Each of the five steps plays an integral role in the result of the undertaking. It effectively resolves the problems currently available in a process and with no specific known solution. For example, the design step identifies improvement objectives from the perspective of the customer and the process owner. It provides necessary information in the approach and defines the measuring step. Variables derived from the established requirements need to be measured using key performance indicators.
Results from the measurements are analyzed to establish insights into the problem. The insights are then used to help design potential solutions that can be implemented. Implementation of proposed solutions is done in the improvement stage. Next, specific solutions are adopted in line with related business processes. Adopted solutions are then monitored to identify changes, if any, and dictate the way forward. Monitoring and deciding the way forward is done in the final step, which is control. If intended goals are not attained, the process is repeated until the desired outcome is attained.
DMADV Technique
DMADV follows a relatively similar approach to DMAIC but how and when solutions are adopted differs. DMADV is an abbreviation for Define, Measure, Analyze, Design and Verify. DMADV aims to identify possible risks and flaws and address them prior to the process's start (Selvi & Majumdar, 2014). It can technically be thought of as a tactic using mitigation strategies in risk management. DMADV is a crucial tool in analyzing the feasibility and practicality of a project or undertaking. As such, the use of DMADV is limited to new processes. Remodels of processes in business process improvement can be considered a domain of application. They refine processes to attain the desired outcome.
DMADV starts by defining the risks that are anticipated in a new process. Quantities that dictate the process are identified alongside the performance indicators. Established quantities are then measured using appropriate and efficient strategies. Results are how prototypes and outcomes will be or function. Efficiency is derived from comparing the observations made to the expectations from the requirements of a new process. Finally, the comparisons are made in the analysis stage. The first three stages are the ones that are similar to DMAIC, with a different perspective.
With the inefficiencies determined, the information is used to tailor a solution. DMADV integrates the solution in the design during the design instead of an existing process. The design stage is associated with the processes in research and development. All processes in process and product design are evaluated as designs before implementation. Verification is the last stage in DMADV. Validating that the established requirements of a new process meet expected standards is done. Upon successfully passing validity and feasibility checks for the proposed solution, a new process is approved.
Six Sigma in Operations Management
Operations management is based on two core components, data, and methods. Methods are crucial in defining and designing processes while data is used in analytics. The methodical approach in both six sigma implementation techniques translates to the value of planning and analytics (Drohomeretski et al., 2014). The existence of analytics requires a predecessor in the form of data. The need for data drives measurements in implementing a quality improvement(s).
Operations management is a dynamic domain that requires to be constantly reviewed and updated where necessary. The six sigma tool extends the process efficiency and improves overall output quality to help boost profit margins by leveraging quality. The total quality management concept using six sigma has had its benefits and challenges. Benefits come from implementing processes that are sustainable in the long term. Challenges arise from the possibility of resource misuse, especially when process improvement starts at optimal levels. Six sigma is inefficient in such a case. New processes may negatively impact productivity or functionality when resources surpass the value created.
Benefits of Six Sigma in Operations Management
Most benefits are directly derived from the necessity of six sigma. Six sigma improves the overall quality of processes by minimizing the wastage of resources. One inefficiency established via business process management (BPM) is that process variables significantly impact process quality. Improving processes, therefore, requires the use of quality management to reduce waste. Quality improvement also increases the value of a product because the outcome will be superior when compared to alternatives.
TQM via six sigma reduces operational costs and increases revenue (Rosemann, de Bruin & Power, 2007). Wastes are significant contributors to inflated material budgets. Reducing waste directly translates to saving costs as the process raw materials are used more efficiently. Superior processes, existing or new, translate to a direct increase in appeal and value. It can be used to justify price increments. Changes in these three domains are the foundation of increasing profit margins and revenue. Increasing the quality of processes boosts employee motivation and time management.
Highly motivated workers are more productive than those with low motivation levels. Human resources are just as necessary as operations management and should be managed efficiently. It is easier for employees to manage their time well and better balance life and work. Better processes mean that outcomes will be superior and, therefore, a competitive advantage for customer loyalty. Current markets indicate a gap between the quality demands of customers.
There is a growing influence of customers in the production process due to substitute products. Businesses and organizations constantly compete with each other to win customers and use six sigma to improve customer loyalty. New customers are likely to stay when they are satisfied with how a company does things. Their loyalty is purely driven by the quality of the product and consistency. Consistency in product quality is defined as a function of sustainable quality derived from implementing six sigma.
Operations Management Challenges and Criticisms
Using data and a plan is a key to success for six sigma implementation. However, this is a significant challenge in some domains because of a shortage of information. Data is used in analytics to derive market variables and the optimal operations parameters. Quality management cannot be effectively adopted in some domains because data is insufficient. The inadequacy of data, or lack thereof, translates to inaccuracies in predictions. More data needs to be collected to counter this problem. The confines and definitions of data collection may contradict the established information management laws in the digital space. Such regulations may limit six sigma in the analysis stage. Information security is also a significant concern in cases where illegal collection or use of data can happen.
When optimization has reached its limit, the law of diminishing returns comes into effect. Beyond a given point, six sigma becomes an expensive endeavor with little to no returns. Some domains can experience resistance to change. Six sigma can be a big step and may ask for more from employees. Such cases are counterproductive when they lower employee motivation, negatively impacting productivity. Quality managers need to know the comprehensive principles and skills of six sigma before applying the tool. Six sigma has rules and applicability parameters that must be adhered to for its successful use.
Change is hard to deal with and must be managed carefully. Management should support change for six sigma implementation success. Deviating from that spells trouble for the process as workers may not be prepared or motivated to align with system changes (Kumar, Antony & Tiwari, 2011). Quality managers are expected to define requirements to ensure no ambiguities comprehensively. There is a chance of experiencing scope creep should a quality manager wrongly define it. All activities involved in implementing quality should be defined accurately. Variations can cause problems in reference. They should be denied well so that others can understand the strategy used to attain the outcomes. Above all, six sigma only works when structured well within the data confines and analytics.
Conclusion
Business processes are always avenues of continuous improvement to increase margins and quality. The tools and techniques used in the process may differ, but the fundamental principles remain primarily similar. Six sigma is a methodology for process improvement that seeks to resolve quality issues based on data. Measurements and analytics make for a more significant part of any approach used. The first step in all methods requires a clear definition of problems and problem points in quality. Refinement of processes to improve them happens in the final two stages. The perspective and time of adoption of quality dictate the approach used. DMAIC is suitable for the iterative development of an existing process, while DMADV is efficient for designing new processes. Overall, advancements in technology have allowed for six sigma to be automated for superior process management.
References
Drohomeretski, E., Gouvea da Costa, S. E., Pinheiro de Lima, E., & Garbuio, P. A. D. R. (2014). Lean, Six Sigma and Lean Six Sigma: an analysis based on operations strategy. International Journal of Production Research, 52(3), 804-824.
Kumar, M., Antony, J., & Tiwari, M. K. (2011). Six Sigma implementation framework for SMEs–a roadmap to manage and sustain the change. International Journal of Production Research, 49(18), 5449-5467.
Rosemann, M., de Bruin, T., & Power, B. (2007). BPM maturity. In Business process management (pp. 322-338). Routledge.
Selvi, K., & Majumdar, R. (2014). Six sigma-overview of DMAIC and DMADV. International Journal of Innovative Science and Modern Engineering, 2(5), 16-19.
Shankar, R. (2009). Process improvement using six sigma: a DMAIC guide. Quality Press.
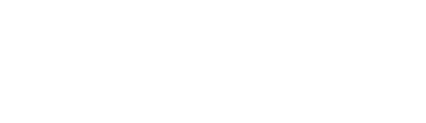
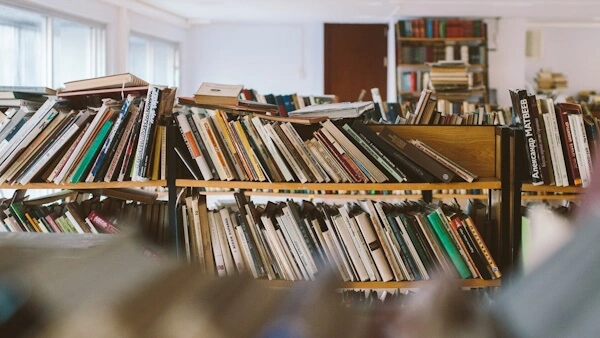

About Author
Tough Essay Due? Hire Tough Essay Writers!
We have subject matter experts ready 24/7 to tackle your specific tasks and deliver them ON TIME, ready to hand in. Our writers have advanced degrees, and they know exactly what’s required to get you the best possible grade.
Find the right expert among 500+
We hire Gradewriters writers from different fields, thoroughly check their credentials, and put them through trials.
View all writers